According to the US GAAP (Generally Accepted Accounting Standards), manufacturing costs are the sum of direct labor costs, direct material costs, and manufacturing overhead costs. Therefore, you might assume, direct labor and material costs are the resources that make the final product. As defined by Investopedia, overhead costs are incurred to make business operations without directly relating to the production of goods. Manufacturing overhead costs are indirect expenses, which are still required to make the final product. For example, those can be factory rent and utilities, manufacturing equipment depreciation, salaries of maintenance team, janitors, and factory management team, to name some.
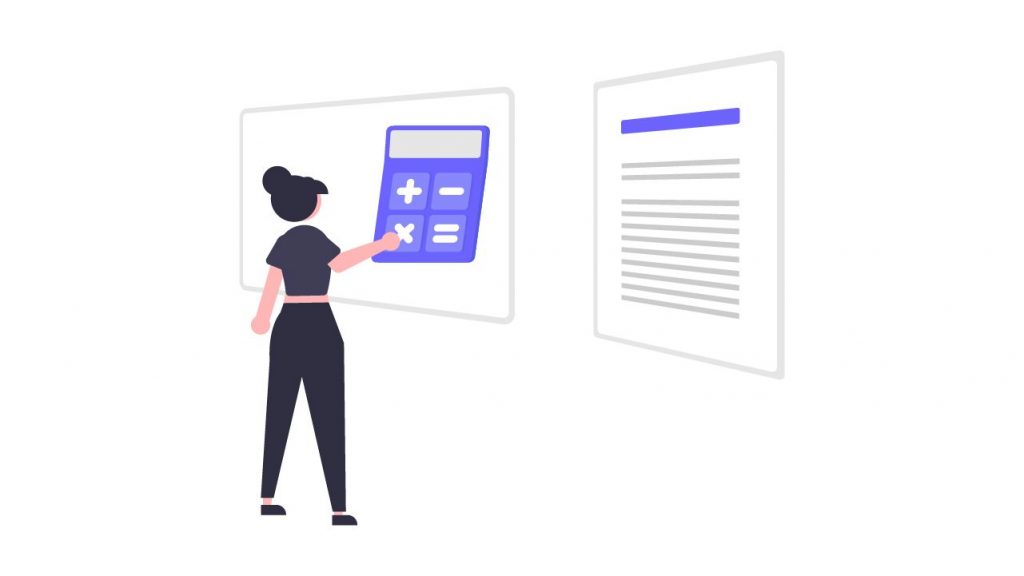
Types of indirect costs related to manufacturing overhead
Manufacturing overhead costs are considered indirect because they cannot be directly traced to each good produced. However, they are still included in the final product costs to calculate final profits. Those costs are allocated to final products based on the overhead absorption rate. Therefore, the overhead absorption rate is calculated by dividing total overhead costs by the number of units for a specific period.
Let’s understand the main types of indirect costs.
Indirect labor
Indirect labor costs are salaries of employees who are not directly involved in a production process, but without whom the manufacturing operations could not be successfully performed. For example, those include security guards, factory managers, supervisors, quality and control specialists, cleaners, etc.
Indirect materials
Indirect materials are used in a manufacturing process but are not directly attributable to a specific product unit. Think of light bulbs, cleaning supplies, stationery, etc. Imagine a fabric factory. Threads are the primary materials for fabric production. So, they will be accounted for as direct material costs. However, irons used to bring them into the final marketable state are indirect materials, which are still required.
Utilities
Utility costs are always there to ensure smooth plant operations. Depending on market demands, businesses update production plans. So, utilities such as gas, electricity, and water costs fluctuate with the number of goods produced. Therefore, cost accountants calculate these costs for the specific period and allocate them to the production units of the same period.
Physical costs
You need essential physical items to implement manufacturing processes. For example, they can be the space or a plant where the production happens, depreciation, required production equipment, maintenance, repair costs, etc.
Financial costs
Financial costs include legal and audit expenses, taxes such as property tax, insurance costs, etc. Those costs are usually fixed, and they are also distributed across the entire production unit.
Fixed, variable, and semi-variable overheads
Overhead costs can be of three types depending on their behavior: fixed, variable, and semi-variable.
Fixed overhead costs
As the name suggests, the costs of this category do not change depending on the quantities produced. For example, that can be rent, property taxes, some salaries, asset depreciation, etc.
Variable overhead costs
Variable costs are directly affected by the business activities and quantities produced. As the production volumes increase, so do the variable overhead costs. These include, for example, indirect material and labor costs, shipping, etc.
Learn about inventory forecasting in our blog.
Semi-variable
Semi-variable costs have a mix of fixed and variable cost characteristics. Generally, there is a fixed cost level defined for a specific quantity of products. However, when the production goes beyond that level, costs start incurring at a variable rate. A good example of that is overtime salary payments.
How to calculate manufacturing overhead cost
Step 1. Calculate the total manufacturing overhead cost
To determine total manufacturing overhead cost, you need to add up all of the overhead costs incurred during a specific period.
Let’s understand it with an example.
Assume that Company XYZ produced a total of 10,000 units during 2020. Following is the overhead expense breakdown for the year 2020:
Expense type | Amount ($) |
Utility | 5,000 |
Insurance | 3,000 |
Indirect labor | 5,000 |
Indirect material | 4,500 |
Cleaning | 1,000 |
Security | 2,000 |
Total | 20,500 |
As you see on a breakdown, the total of all overhead costs is USD 20,500.
Step 2. Determine the manufacturing overhead cost per unit
To find the overhead unit cost, you should divide the total amount of manufacturing overhead costs by the number of units produced during the same period.
Following the case mentioned above, we should divide USD 20,500 by 10,000 to find the production overhead cost per unit. Performing this calculation, we get that the price is USD 2.05 per unit. So, for each unit produced, Company XYZ spends $2.05 on manufacturing overheads.
The importance of manufacturing overhead cost allocation
Like all other expenses, overheads have a direct impact on a company’s financial statements and profits. So, continuous tracking and accurate allocations of those expenses are crucial for successful business operations and profitable outcomes. Those are of enormous importance when it comes to pricing decisions, budgeting, efficiency and effectiveness controls, etc.
The regular tracking of production overheads sets proper monitoring over manufacturing productivity. It is a measure that estimates the effectiveness of production inputs in relation to the levels of outputs. Therefore, businesses can use this analysis to control the percentage of revenue that goes into the production overhead costs.
Overall, this figure is an indicator of the performance of business operations. If the ratio is low, it means that the business effectively utilizes resources. Therefore, the opposite means ineffective spendings and is a warning that business and supply chain processes should be reviewed.
To sum up
Manufacturing overhead costs are an unavoidable part of running a production. Therefore, those costs should be under constant review and control to ensure that manufacturing processes are effective and no unnecessarily high expenses occur. It is always important to remember that cost management is a crucial part of business health and success.