Choosing the right inventory costing method is critical for stock management, order fulfillment, and overall manufacturing organization to grasp the cost of products sold. This helps the business to be successful in the long run.
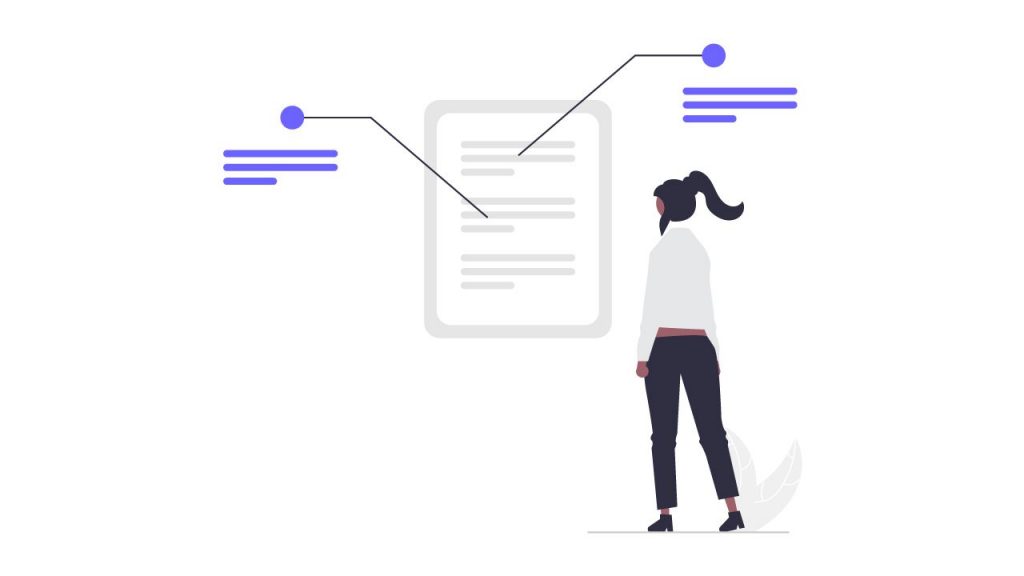
The process of allocating value to inventory, hence the cost of items sold, is known as inventory costing.
It is a strategy that helps to have a precise inventory management. With it, companies and organizations can lower overall inventory costs and help determine how much a business should store with accurate inventory management in place. All of this data allows businesses to choose the required margins for each product or product category.
Which Inventory Costing Method is Right for You?
It is imperative to understand that methodology used by businesses to determine the value of their inventories can directly impact the revenue and value of stocks shown in their financial statements. Each company should have a precise strategy for estimating and reporting inventory and use it systematically. Moreover, regulators expect firms to employ the same methodology for calculations, so it is essential to choose it wisely.
Below find the main costing strategies.
First in First Out (FIFO)
FIFO is the acronym for “First-In, First-Out”. This methodology presupposes that items that are generated and acquired first are sold first. This is the method used to assume a cost stream when calculating the cost of goods sold.
The FIFO methodology is considered one of the most reliable ones because of several reasons. First of all, the FIFO strategy is simple to comprehend, widely acknowledged, and relied upon.
Moreover, it reduces waste as you will always be moving out the oldest inventory first. The remaining inventory will be a more accurate representation of market value. This is because unsold stocks have been produced recently. With the FIFO strategy, you will generate more profit and have a more precise financial picture of your business.
How to calculate with FIFO methodology?
First, you will need to determine the cost of your oldest inventory to compute COGS (Cost of Goods Sold) using the FIFO technique. Next, multiply that cost by the number of items sold.
Remember that the term “inventory sold” applies to the cost of items acquired for resale or the cost of products created, including material and production overhead expenses.
Also, consider that the firm’s inventory pricing can vary, and you should factor that into the equation.
For example, if a company sold 300 units of an item, 150 units were purchased at $20, and 50 items were acquired at $25, the company cannot apply the $20 cost price to every unit sold.
It is essential to consider that only 150 pieces are available, and the company must allocate the remaining 50 products to the higher, $25 pricing. Last but not least, the product must have been sold to be included in the calculation as businesses cannot factor the unsold inventory into the cost of goods calculation.
Last in, first-out (LIFO)
Another methodology to calculate inventory costs is LIFO. The LIFO stands for Last in, first-out (LIFO). It is a system of inventory accounting in which the most recently manufactured products are sold first. To compute COGS (Cost of Goods Sold) using the LIFO technique, you will need to determine the cost of your most current inventory and multiply the number of units sold.
It is essential to understand that LIFO cost accounting may help almost any sector dealing with escalating expenses. It is specifically beneficial for businesses that offer items that increase in price every year. With LIFO methodology, a company can better balance its income to its most recent costs when prices rise. For instance, supermarkets and pharmacies employ LIFO cost accounting since practically every item they carry is subject to inflation. Moreover, companies can also save money on taxes they would have paid under alternative cost accounting methods.
Average cost method
Another inventory valuation method is called the average cost technique.
The average cost approach will require the least resources of all the other valuation methods since it needs the least labor to implement.
Moreover, with this method, income cannot be changed as quickly as other inventory costing methods. The average cost method is especially beneficial for companies that offer identical items or those who find it difficult to determine the cost of individual units.
How to calculate with Average cost methodology?
The average cost approach involves a baseline average of all similar products in inventory, regardless of the date of purchase, and then calculating the final inventory items at the end of the reporting period. The value of the products available for sale is calculated by multiplying the average unit cost by the last inventory count. The exact average price is applied to the number of goods sold in the previous reporting period to calculate the cost of goods sold.
How can excess inventory be damaging for your business?
Now that you know how to calculate the cost of your inventory with different methodologies, it is time to question why too much stock can be damaging for your business.
While having excess inventory on hand can bring many benefits like obtaining bulk-purchasing discounts and responding to changes in client demand, some drawbacks are crucial to consider when establishing an inventory control strategy.
Below find some of the side-effects of having excess inventory on hand.
Perishable inventory
When you overstock your inventory of perishable goods, they tend to languish in the warehouse after the expected shelf life. Food businesses, for instance, are unable to offer obsolete products due to the health and safety risks of consumers. Overstocking in certain circumstances leads to products that must be thrown away, resulting in a waste of financial resources.
Storage issues
Overstocking will eventually occupy space in your warehouse and require additional resources for maintenance. It will take up valuable floor space, preventing you from acquiring new products. Moreover, it is essential to consider that consumer demand for products can change over time. Things that remain in inventory for a few months might become outdated, especially when it comes to fashion items. What once was trendy can instantly become obsolete and worthless.
Financial challenges
It is essential to consider that investing too much in inventory may rapidly lead to a cash-flow problem, especially if products are languishing in storage and not being sold for a profit. Such situations are undesirable for any business. Furthermore, a cash flow deficiency may force your company to borrow money and pay interest on that loan. Another drawback is the lack of cash flow. It might prevent your company from taking advantage of possibilities that need capital production.
What are the main costs that refer to inventory?
Ordering expenses are the costs you will have each time you arrange an order with your supplier. Ordering costs include payroll taxes, transportation costs, the salary of the procurement department, expenses related to finding vendors, receiving expenses, costs of electronic data interchange (EDI), to name a few. These expenses are typically accounted for in an overhead pool and assigned to the number of units produced each quarter.
Inventory storage costs
Inventory storage costs are the amount of rent a company pays for the warehouse stores its product. This can be all the direct rent for all warehouses. As another example, it can be a portion of the total rent for office space used to store goods. Maintenance costs include warehouse space, inventory management services, inventory risk costs, and inventory financing, to name a few.
How much inventory should I start with?
It is crucial to understand that the rules change from industry to industry. You need to acknowledge that if you are going to deal with perishable items, you need to make sure that you can sell all goods before they go obsolete. Even if you are not dealing with perishable products, and for instance, you are planning to sell clothing, you have to consider the influence of current trends on your sales.
It is also essential to keep an eye on the sales volume of different sorts of products.
Often some products can sell better than others but do not hurry to re-order. You have to estimate whether the potential advantages or profit exceed the risk.
It’s critical to evaluate how much you can afford to spend before deciding on more significant quantities or new items.
Otherwise, you may end up investing in things you won’t end up selling.
Keep in mind that investing in additional inventory may result in higher profitability only if the items are sold. Another major factor that you should consider is the turnover ratio. It is essential to consistently estimate the worth of your inventory while calculating your turnover rate. You need to determine how many items you sold and the replaced products in a certain period.
Before You Go
Last but not least, you will need to have a precise inventory management system in place to make you up to date about your inventory. With modern inventory management software like eSwap, it is easier than ever before. The advanced features and functionalities of eSwap will help you reduce the number of time-consuming manual processes.
With the eSwap inventory management system, you will be able to track and manage all inventory movements across your supply chain and warehouses, such as picking, packaging, shipping, and receiving new stock, among other things.