With a limited product turnover, inventory management can be an easy, sometimes even manual task for a starting company. However, as your business progresses, you can’t enjoy the luxury of simple inventory management anymore.
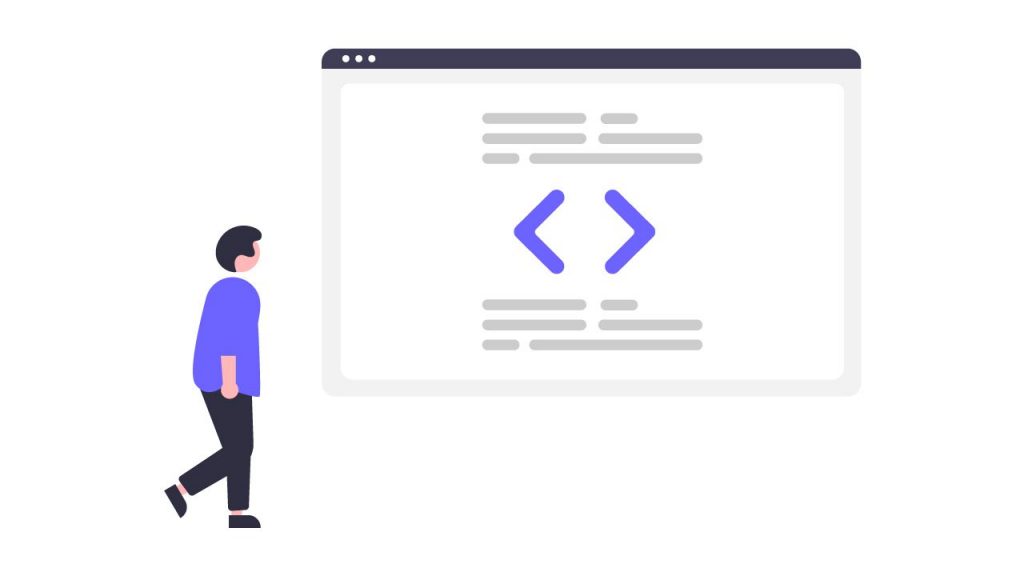
There are a lot of factors that can change your inventory status; demand and price fluctuations, shifts in consumer behavior, prices of raw materials, etc. Keeping everything on track among that variety of impacting factors might be a daunting prospect.
That’s why there are several techniques for implementing inventory control, and SDE analysis is one of them.
We guess, right now, you are questioning the SDE meaning. So let’s answer you right away.
What is SDE?
SDE is a warehouse classification technique that helps categorize the available inventory items into groups, making inventory control more accessible. If you are curious about what SDE stands for, here is the answer.
SCARCE: The first inventory category in SDE analysis is scarce. It shows the relatively more complex products to acquire, as they arrive late, undergo some processes before reaching the inventory, and similar. The classic example of scarce products includes imported products. You should wait for them to arrive, and they should pass the government control before being approved for entering the country.
DIFFICULT: Next comes the category of complicated products. They are produced in a domestic market but are not easy to acquire. These inventory items take a long time to produce and bring to the warehouse, as their production process takes time, there is a scarcity of manufacturers or reliable suppliers and many more. Usually, difficult products are those which require from two weeks to six months to arrive.
EASY: Last but not least, the last category of SDE analysis is for easy products. Easy items are produced locally; they do not require much time or resources to produce, and therefore are freely available anytime you need something. Take pens, pencils, and other office supplies store products, as an example. As you might guess, those products cause no difficulties when ordering them.
SDE analysis helps improve the procurement processes
You can better understand the SDE meaning if you view it in the procurement processes.
Suppose you have a procurement period ahead and want to plan your stock to avoid overstocking or understocking issues. This means you want to arrange your inventory so that there are always enough items in place, and you don’t have problems lacking the inventory space or failing to meet your customer’s demand.
So, what should you do in that case?
Here is when SDE analysis comes in handy. Instead of guesswork your future orders, you can classify all the products you will need during the year with the SDE analysis. Further, by knowing the difficulty of acquiring each product, you will see how you arrange your orders.
Examples to grasp it better
Suppose you need products for the New Year, which are not produced in your country, and you need to order them. As you know in advance that you will need those products at the end of December, and as you know, it might take months for the ordered products to reach your county, you can set the order date correctly.
If you know it will take some four months for a product to be produced and shipped to you, you will order it in the middle of August or the start of September. In this case, the products are classified into difficult.
We can also discuss the SDE meaning from the opposite end. If you need some local products along with the above-mentioned imported products, the planning should be done differently. In this case, you should understand the time it takes to restock those products.
If it takes several weeks to receive those inventory items, you should order them approximately a month ahead. If you know your needed goods are always available, you shouldn’t bother ordering them in advance.
Are there any drawbacks of SDE analysis?
You have already grasped the SDE meaning and its benefits; however, the method also comes with its tradeoffs. We would prefer not to call it a drawback but rather a thing to consider – you should not rely on SDE inventory analysis as a tool for an in-depth analysis.
Though it can help you figure out the vague future of procurement planning, SDE inventory analysis works on the surface.
It does not give you thorough information about each product category. You should update each product’s manufacturing and shipment time from time to time to ensure you don’t plan your purchases based on outdated data.
Use automated software for better inventory planning
If you want more precise data to rely on for your inventory planning, we suggest you use professional inventory management software. With the help of the software, you can receive detailed analytics and report on all your stocks in all locations.
This way, you can track the previous years’ data to plan your current and future procurement processes accordingly.
Not sure how to start the inventory automation journey for your business?
Start a 14-day free trial in eSwap to give it a try!