What Is an Inventory Audit? Procedures & Methods
Metrics are too vital for wholesale and retail businesses. That’s what an inventory audit is for. It’s a physical check of your merchandise against what’s in your records to verify the accuracy of your internal and external assets. The audit also includes an analysis of a company’s inventory management procedures.
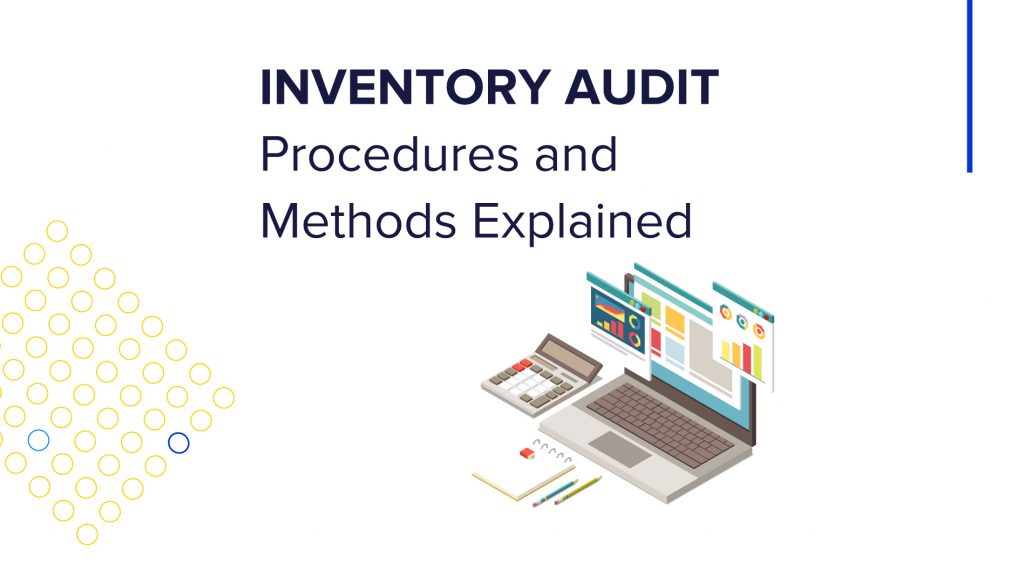
While inventory is an irreplaceable part of business, it is also very costly. IMPO Mag US research shows that inventory, accounts receivable, and accounts payable have tied up over $1.1 trillion in cash. This is equivalent to 7% of the US GDP, i.e., a considerable amount of cash that could be used for other purposes if it were not needed to maintain inventories. That said, inventory audit procedures are essential for businesses greatly relying on materials.
What Is Inventory Audit?
Before we proceed with the substantive procedures for an inventory audit, let’s first answer the question, “what is an inventory audit?” In simple terms, it’s a stock assessment conducted by an auditor. The auditor’s objective is to ensure that the client’s inventory records are accurate and that the financial statements are free from material misstatement.
Lack of Inventory Audit Procedures
Companies lacking efficient inventory management practices often face various problems. Let’s examine the main challenges a company may face without monitoring procedures.
- Inability to track what items are in stock and what needs to be restocked
- Poor inventory turnover rate
- Wasted money on obsolete or unsellable inventory
- Unhappy customers due to stockouts
- Poor working capital management
How can it affect your business? The whole idea of auditing is to check and prevent such mistakes by keeping international standards. Some of them are IFRS and GAAP.
Companies That Don’t Require Inventory Audits Procedures
Although all businesses can benefit from an inventory audit, some may not require one. For example, if your company is family-owned and not publicly traded, you may not be required to invest resources into hiring an auditor or investing in inventory management software.
However, suppose your company is expanding and you plan to seek financing from investors or lenders. In that case, they will likely require an inventory audit as part of their due diligence. The AICPA Auditing Standards, a company must have an audit if its inventory is material to a company’s financial statements. An employee responsible for the management should collect sufficient evidence regarding the conditions and overall count of the inventory.
- Audit procedures include:
- Physical inventory counting
- Evaluation and inspection of the results achieved by physical countings
- Test counts
- Audit procedures over the final records to determine the accuracy
Audit records must be accurate, transparent and objective to help the business owners and investors make informed decisions.
So, what methods and techniques can you use to gather the precise data?
Inventory Audit Procedures & Methods
Substantive and analytical procedures are two approaches to an inventory audit. The first one is more mechanical and involves directly counting items in stock and comparing them to what is recorded in the books. Substantive inventory audit procedures are physical examinations of a sample of the merchandise in your store or warehouse. The auditor will look at what’s on your shelves and compare it to what’s in your books.
On the other hand, analytical audit procedures are more cerebral and involve using accounting ratios and trends to understand the client’s inventory levels. This is done by analyzing historical data and making assumptions about the client’s inventory levels.
Both approaches have their pros and cons. Still, they complement each other. The substantive audit procedures collect data which is later proceeded and analyzed.
Analytical Inventory Audits: Main Methods and Techniques
Analytical audits are often based on financial metrics, including but not limited to:
- Gross margins
- Inventory turnover ratio
- Days inventory on hand
- Historical costs of stock
An auditor may use various techniques to analyze data gathered with a substantive approach. We will further examine some of the most common ones to understand the analytical inventory audit better.
Cut-off Analysis
The method’s name speaks for itself. Audit procedures imply that no inventory item can leave or enter the warehouse during the counting. It ensures the absence of mistakenly handled items. While the cut-off analysis doesn’t allow retailers to audit their inventory thoroughly, it provides a snapshot of what was in the store or warehouse at a specific time.
This method helps ensure that all inventory items purchased or manufactured have been properly recorded in the accounting records. The auditors review the client’s purchasing and receiving records to ensure that all items are present in the accounting sheets.
Cost Variance Analysis
This analytical procedure involves investing in an accounting tool to investigate possible budgeting irregularities. The system uses the prices of similar items in the market to check whether the client’s inventory is overvalued or undervalued.
Moreover, with the help of cost variance analysis, retailers can determine the difference between the allocated budgets and the money spent for specific purposes.
The auditor will look for explanations if there is a significant difference between what the client paid for and what they should have paid. The auditor will adjust the client’s inventory records if the business owners can’t provide a reasonable explanation. Retailers use this analytical procedure to ensure that their inventory is valued correctly.
ABC Analysis
The main component of the ABC analysis (also called high-value item inventory) is grouping. The employee group inventory with various values. There is high-value, mid-value and low-value inventory. ABC analysis implies a cycle count approach to inventory audit, i.e., counting all inventory but not at the same time. Counting high-value items are much more frequent than the low-value inventory audits.
Such an analytical procedure streamlines the inventory audit process and focuses on the business’s most critical and successful items.
The method works like this:
High-value items are in A listings. Mid-value items refer to B groups. Low-value items are in group C accordingly. As for their stocking, it also differs according to the groups. Place the C group items in bulk to save storage space. The A group items should be easily accessible but in secure locations for quick access.
Freight Cost Analysis
Freight cost analysis considers the shipping (freight costs) needed for inventory transportation. Inventory value usually includes these costs as they are essential for businesses to get the product to the customer.
The auditor will analyze all the client’s invoices to ensure that all freight charges have been appropriately accounted for.
Thus, the records refer to the time of sending your items and when they arrived at the desired destination. This method hugely helps to record lost or damaged items as it can affect the client’s income.
Inventory Obsolescence Analysis
The auditor will also assess whether the client has too much inventory on hand that is not selling. This is what we call inventory obsolescence. The term refers to “excessive” or “dead” inventory. These are products that retailers cannot sell due to many reasons:
- Style is out of date
- The product is no longer needed or used
- A new and improved product has superseded it
- There has been a change in consumer tastes or preferences
… and so on.
The inventory obsolescence analysis is based on the correlation between inventory demand and inventory age. The graphic below depicts how age and demand determine whether inventory is slow-moving, excessive, active or aged.
Finished Goods Cost Analysis
This method refers to the finished goods assessment and analysis. It includes cost analysis, usually connected to the makers. In the cost of finished goods, we understand all the expenses on the way. To find the finished goods inventory, an auditor needs the following data:
- Beginning inventory of finished goods
- COGM or cost of goods manufactured
- COGS or cost of goods sold
Tip: There are also specialized courses that can help auditors learn more about calculating each data and finding the cost of actual goods.
After getting all the needed information, an auditor can easily find the cost of producing one unit and the total cost of all the units sold during the review period.
This procedure is essential to businesses because it helps them understand what they need to do to improve their product and the main expenses. It also allows companies to see if they are selling their products at a profit or not.
Overhead Analysis
Such an inventory audit analyzes indirect and overhead costs making the inventory prices. This is not necessarily a required procedure, but it is still popular among businesses that want to have a better understanding of what their indirect costs are.
To determine the overhead cost, an auditor needs to analyze and review the client’s general ledger. It will help to identify all the expenses a company should or should not include in inventory prices.
Those cost analyses (rent or utilities) can help to predict additional costs as part of inventory costs. It will definitely assist with budgeting and planning.
Additional Solution: There are other effective inventory management strategies that will help retailers upscale their businesses and become more profitable.
Automate the Counting With Inventory Audit Software!
Several years ago, businesses had no advanced options. Professionals had to implement stock audits on sheets of paper or in excel files. The risk of human error was extremely high.
Nowadays, we have a much better solution that doesn’t require businesses to waste time and money on inventory audits.
Specialized software does all the hard work for you by automatically counting stock and providing real-time data that is always accurate. This way, businesses can focus on what’s important – selling products and making a profit!
Solutions like eSwap help eCommerce retailers store all their inventory data in one place. This includes product information, supplier details, stock levels, and order history.
Moreover, eSwap, as one of these kinds of software, supports analytics and accounting features that will help you with the audit process. Find detailed information in the Help block as well. Investing in such a tool is a cost-effective decision that will save you time and money in the long run!
Closing Points
To sum up, an inventory audit is necessary for businesses that want to ensure they are selling products at a profit. Various methods and strategies can help assess and analyze inventory.
The most important thing is to choose the right method for your business and invest in inventory audit software to automate the counting process!
eSwap is advanced software that will help you with inventory management and provide accurate data for your inventory audit. Schedule a demo with us today to see how eSwap can help your business!