Inventory costs include all the costs that the seller incurs to order, handle, store, and administer inventory. The sellers must estimate these costs accurately to avoid losses during the fiscal year.
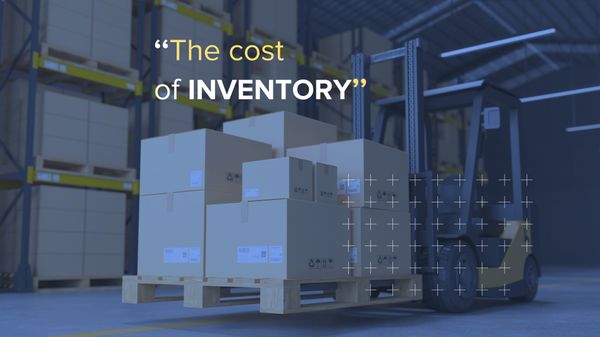
Although describing the term is pretty straightforward, some business people find it challenging to calculate inventory costs. To simplify the process, accountants divide inventory costs into three main categories: ordering costs, carrying costs, and shortage costs. The other types of inventory costs closely relate to the above-mentioned.
3 Categories of Inventory Costs
Ordering Costs
Any costs associated with ordering the inventory are referred to as ordering costs.
Clerical expenses such as payments, taxes, accounting, and communication present some part of order costs and derive from placing the order. If you are supplying similar products that do not vary significantly, your clerical expenses would be fixed most of the time.
Transportation expenses are another portion of ordering costs incurred by moving the inventory from the manufacturer’s location to the warehouses. Unlike clerical expenses, transportation expenses may frequently vary if you buy stock from different manufacturers and, therefore, various locations.
Receiving costs occur after you receive the inventory you have ordered. A team of workers inspects the inventory to ensure the goods have been delivered in safe and sound conditions.
The last part of your ordering costs of electronic data interchange (EDI). If you have a relatively larger business, you will likely face these expenses and prefer using specialized systems to reduce your overall ordering costs.
Carrying Costs
Carrying costs, also known as holding costs, are the expenses that relate to maintaining and storing the purchased inventory—the larger your inventory amount, the higher your carrying costs since you will need more storage.
Storage costs are the most relevant component of carrying costs and comprise a significant portion of them. They include the facility maintenance costs, the rent or the purchase amount of the warehouse, utility payments, etc.
Inventory financing costs represent the expenses associated with investing in the maintenance and holding of the inventory. These include labor costs, costs incurred for purchasing the necessary material for specific inventory items, etc.
Inventory services and risk costs include the expenses that cover the insurance and security costs and the costs associated with possible risks of inventory. Those could be breakage, shrinkage, or any other risk that may cause inventory damage before selling it to the customer.
Shortage Or Stock Out Costs
Stockout costs involve the expenses that sellers incur to overcome the challenges brought by the stock-out. The latter occurs when the company runs out of necessary stock to supply its customers. Therefore, sellers may add intermediaries such as distributors to make the process faster, ask the manufacturers to ship the inventory faster by paying them higher prices, etc. Whichever solution the sellers come up with, they will have to face certain expenses brought by the shortage.
How To Minimize Inventory Costs?
After learning the categories and types of costs that you may encounter as a seller while managing your inventory, it is always useful to learn how you could minimize these costs.
Learn The Specifics of Your Product
If you know every aspect of your product, managing is as a part of inventory would be easier. For instance, if your product is perishable, you should store it at a certain temperature. Examples like this demonstrate your knowledge of the inventory and the techniques you apply to manage it efficiently.
Train Your Team Consistently
As your business grows and your inventory amount increases, you want to have skillful and dedicated team members that would invest in the proper inventory management. Inviting weekly meetings, conducting team training, or organizing employee assessments are some ways in which you could warm your team up. Moreover, you should demonstrate appreciation for their hard work by distributing commissions and bonuses based on their performance.
Prepare Inventory Reports
The larger your business, the more difficult it is to track your inventory progress and evaluate its performance. However, since this is a crucial factor for succeeding in inventory management, you should always prepare inventory reports as a seller and analyze your inventory progress on time. This will allow you to understand the products that sell faster and the ones that require more time. Consequently, you will be able to conduct the necessary operations to store products with different selling patterns separately.
What Is The Best Way To Manage Inventory?
To prepare detailed inventory reports and keep track of your inventory consistently, you need to automate your inventory management processes. You can use eSwap to start your inventory automation.
With the platform, you can track your inventory in multiple warehouses and move items from one warehouse to another with a single click.
This will save enormous amounts of time for you. Furthermore, you will be getting real-time updates about your inventory progress. The system will regularly generate inventory reports for you on a single secure platform.
To start using eSwap, sign up here for a 14-day free trial.
Conclusion
The costs that sellers incur to order, handle, and maintain inventory, are inventory costs. Its main categories are ordering, carrying, and shortage costs. Other expenses deriving from the main cost categories include clerical, transportation, receiving, storage, inventory financing, and inventory service and risk expenses.
To minimize inventory costs by enhancing your inventory management, you can use eSwap as an inventory management tool.