Inventory management is a critical aspect of any business – it’s what keeps you running and keeps your products in stock. If you want to ensure that the manufacturing process is smooth and your income is high, you need to invest in a computerized inventory management system. That’s when an MRP system comes in handy. Materials requirement planning allows manufacturers to plan, manage and control their inventory flow more effectively. MRP systems can be very beneficial to your business. However, they do come with a few drawbacks you should consider.
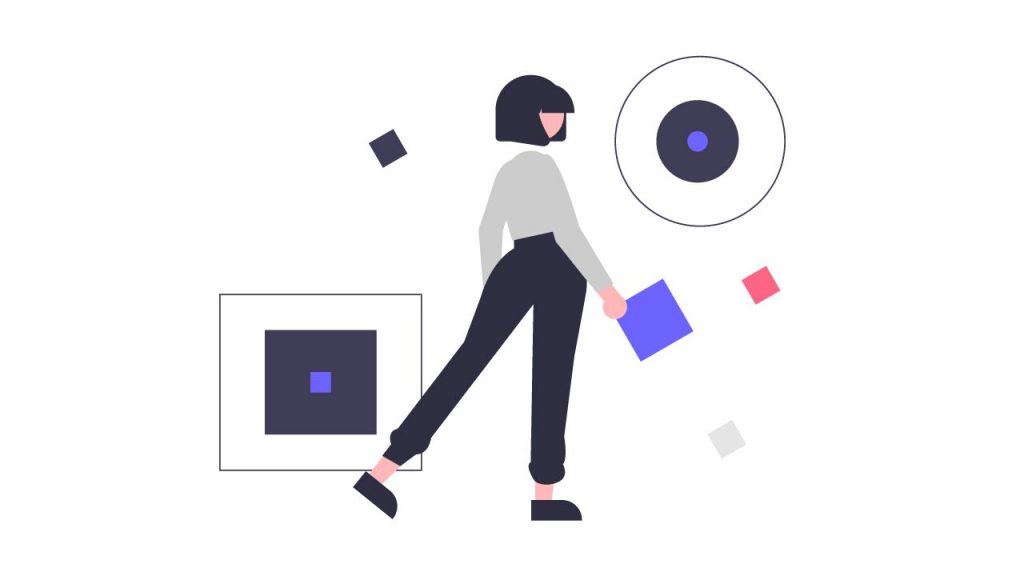
What Is Materials Requirement Planning?
MRP stands for materials requirement planning – a system that uses algorithms to generate information about what materials are required when they and in what quantity. The system helps to streamline inventory management and keep track of stock levels. That’s why MRP systems are great for use in manufacturing companies. Moreover, they can be useful for any business that needs to manage its inventory flow.
How Does MRP Work?
The main features of materials requirement planning include:
- Demand forecasting
- Purchase planning
- Bill of materials (BOM)
Demand Forecasting
Demand forecasting is a substantial component of MRP. The essence of this feature is to determine the type and quantity of materials necessary for the smooth manufacturing process. Accurate predictions are the key to preventing inventory issues, such as overstocking or overselling.
Purchase Planning
Another core feature of MRP is the purchase planning that determines the sourcing of raw materials. The system automatically detects the lack of particular products and helps a company’s purchasing department better understand what is needed to fulfill specific tasks and orders.
Bill of Materials (BOM)
Another tool used by the MRP system is the bill of materials. It is a hierarchical list of all the materials, including subassemblies and every component needed for manufacturing. In the BOM, all the inventory is classified into independent demand of dependent demand items. Independent demand items are the final goods presented at the top of the BOM hierarchy. Dependent items, on the contrary, are the raw materials used in manufacturing.
4 Major Steps in Materials Requirement Planning
Step 1: Identifying the Requirements
At the beginning of planning, the software identifies the customer demand and needs. Further, the process starts with inputting customer orders and sales forecasts. Note that the operation of your MRP system depends on the quality of your provided data.
Once the requirements are identified, the system looks for any subassemblies needed for satisfying each requirement.
Step 2: Inventory Analysis
MRP systems are easily connected to your inventory management software, meaning they can detect the status of items available in stock. Moreover, due to modern technologies, MRP systems can detect and keep track of inventory not physically available in the warehouse.
Step 3: Scheduling
At this stage, the MRP systems determine the time and resources required for a particular step of inventory management. Thanks to scheduling, the production workflow occurs smoothly without any delays. As a result, there are no canceled orders, and the customer satisfaction rates increase.
Step 4: Recommendations
In case of delays or other issues connected with the product management process, MRP systems can automatically keep you alerted. Moreover, the system calculates the possible solutions performing what-if analyses.
The Pros of MRP Systems
Why is MRP necessary? Due to the highly integrated system, businesses get more visibility into their inventory requirements to keep the balance between demand and supply. Without detailed and precise information, companies risk running out of stock. Speaking of good, there are several benefits to using materials requirement planning in your business:
Increased Efficiency
MRP systems help companies become more efficient by automatically generating production schedules and purchase orders. Thus, the retailers can plan their production processes more accurately and always have the necessary materials on hand.
Better Inventory Control
With an MRP system in place, retailers can track their inventory levels more closely and ensure that they are not overstocking or understocking any items. Therefore, it helps to reduce the amount of waste produced by a business.
More Time for Planning
By automating some of the tasks associated with inventory management, businesses can free up time to spend on more strategic planning.
The Cons of MRP Systems
There are a few downsides to materials requirement planning that you should be aware of before implementing such a system in your business:
High Upfront Cost
One of the most significant disadvantages of MRP is the price. These systems can be expensive to set up and maintain, so materials requirement planning may not be a good fit for businesses on a tight budget.
Inflexible
MRP systems are often very inflexible, meaning that changes to production schedules or inventory levels can be challenging. Such methods may be challenging for businesses that need to adapt quickly to market changes.
Requires Expertise
Businesses need to have a well-trained staff who will know how to use the software efficiently to use an MRP system effectively. Unfortunately, not all small companies can afford this because of a lack of resources to hire and train experts.
MRP vs. ERP
MRP and ERP complement each other in optimizing various business operations. MRP is a subsystem of an ERP system providing the corresponding departments with valuable information concerning materials and resources.
The main difference between materials requirement planning and enterprise resource planning is that the latter helps to plan and automate back-office functions, like settlements, IT services, or regulatory compliance. Consequently, investing in enterprise resource planning systems is advantageous if a company needs to optimize accounting, human resources, and more management spheres. The MRP systems are more focused on materials management.
Both systems can be applied simultaneously in the same company. Employees from various departments may find using ERP systems beneficial. However, MRP tools are only for people dealing with manufacturing operations. Before choosing between the two systems, note that MRP and ERP can be complex and expensive to implement. So, it is helpful to consult with an inventory management specialist before deciding.
Closing Points
With the ever-expanding industry of eCommerce, the market is full of various unique techniques and inventory management strategies. This makes materials requirement planning one of the most effective tools for businesses of all sizes. Understanding the main features and benefits of MRP, you can make informed decisions about whether or not this system is suitable for your company. Moreover, MRP can help you build a steady manufacturing network with increased efficiency, better inventory control, and more time for strategic planning.