If you’re running an inventory, you know that stockouts (not having any product to sell) can be a death sentence for your business. To avoid such a tragic outcome, eCommerce companies should spare time to learn about two fundamental constituent phenomena: reorder point and safety stock. While they may seem similar at first glance, there is a distinction between the two terms. Calculating your brand’s reorder point vs safety stock is essential for running your inventory management successfully.
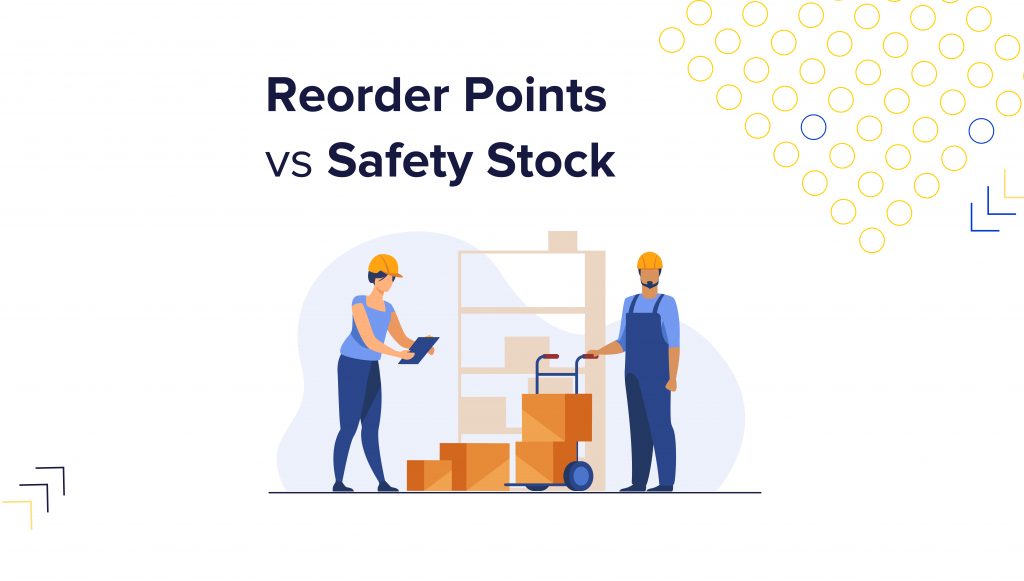
To help you get your head around reorder point (ROP) and safety stock, we’ll define each and explore their core differences and role in inventory management.
General Overview: Key Statistics
In fact, inventory is the core asset of any company operating in the eCommerce industry. Still, over 43% of small businesses do not track inventory levels. This may lead to substantial financial losses and inefficiencies. Retailers tend to lose hundreds of thousands, if not millions, of dollars on inventory each year. For instance, stockouts through the Black Friday sales cost retailers over $4.6 billion in lost sales in 2021 alone. With stockouts as the primary cause of lost sales, it is crucial to understand how reordering points and safety stock help avoid them.
Even eCommerce giants such as Ralph Lauren have seen the perils of inadequate inventory management, famously losing over 50% of its annual profit in 2015 and 2016. Poor inventory management may result in unprecedented losses from overstocking or little inventory.
Inventory control is the proactive and reactive process that ensures you have the right stock level at the right time. Companies lacking sufficient means and resources to track inventory levels can quickly find themselves in hot water when demands unexpectedly spike or drop.
Both proactive and reactive management processes help businesses avoid such issues. Reorder point (ROP) is a proactive measure, while safety stock refers to reactive inventory management.
Reorder Point Defined
The reorder point (ROP) is the minimal number of units a company must have in stock to avoid stockouts and assure order fulfillment. When inventory levels approach the reorder point, the replenishment procedure implies restocking the item. The primary objective of reorder point is to ensure that your company can maintain inventory at a level that consistently meets consumer demand.
Treat it as a specific trigger point at which you need to place a new order for more inventory to avoid any stockouts. The reorder point is generally based on prior sales to help you anticipate the item’s future sales. While most companies order inventory based on past sales, some also consider future trends when calculating the data.
Reorder Point Planning Tips
Reorder point planning is about anticipating future customer demand and stocking enough inventory to meet it. Retailers looking for efficient solutions may invest in inventory management software to help them predict future demand and, as a result, calculate accurate reorder points.
Reordering Rules in eSwap
Smart technologies help retailers reduce stress related to inventory management and decrease the time needed to place new reorders. Tools like eSwap are designed to ease reordering by helping you predict future customer demand. With eSwap, you can set specific reorder rules for each product.
When the inventory levels are low, eSwap will automatically place a reorder for you. Reordering rules streamline the process and make it as effortless as possible.
Here’s how to set specific rules for each product listed on eSwap:
Step #1 Choose the product you would like to set specific reorder rules
Step #2 Click on the Reorder Rules tab on the top of the page opened
Step #3 Tap on the Create Reorder Rule button and fill in the corresponding information
The platform will ask you to fill in the following fields specifying:
- Warehouse where the stock levels should be updated after creating a purchase order
- Company that should appear in the PO lists
- Vendor from who you will buy the items
- Pricelist currency
- A minimum stock quantity that should trigger a purchase order
- Reorder quantity
Don’t forget to calculate and consider every detail of the reorder point. This will help you avoid significant lag periods and reduce the possibility of back-ordered popular products.
Safety Stock Defined
It is essentially an extra inventory that a firm keeps on hand to avoid running out of stock. Safety stock is crucial, especially if you’ve overestimated the reorder threshold or there is a supply chain failure. It will help you satisfy customer demand and deliver orders according to the deadlines, keeping your customers satisfied.
Safety stocks are exceptionally efficient for items and products that are popular and in high demand. An excess supply of the most popular things in the warehouse will ensure that requests for such products are filled as soon as possible.
Still, keeping a balance means avoiding over-purchasing products that are rather unpopular than in high demand. It can result in unnecessary financial expenses for storing and marketing excess units.
Therefore, you should consider stocking up on things more likely to run out frequently while keeping unpopular items at minimum stock levels.
Safety Stock Planning Tips
Planning and scheduling are integral to success. Before anything else, retailers must evaluate the risks and opportunities involved in manufacturing or selling a product. After that, they can develop an inventory management strategy that will help them mitigate risks.
A company’s safety stock levels should be based on customer demand and historical data.
Analyze Customer Demand
Customers are the bread and butter of every business. Understanding customer demand is, therefore, critical to success. There are a few ways to analyze customer demand:
- Look at past sales data
- Use market research
- Utilize customer surveys
People tend to buy more of some products during specific seasons. For example, they buy more sweaters in winter than in summer. As a result, businesses that keep track of customer demand can stock up on inventory before the peak season. This way, they won’t run out of items when customers need them the most.
It may sound too obvious to mention but bear this point in mind to avoid any future issues.
Historical Data Overview
Retailers can use past data to predict future customer demand. Purchase history data is an excellent way to understand what customers want and when they need it. Businesses can use this information to develop a safety stock plan that meets their brand identity and customer preferences.
Reorder Point vs. Safety Stock
Critical Factors Essential for Reorder Level
It is essential to understand that the reorder point varies for each product and is heavily impacted by two crucial factors: daily sales velocity and lead time.
Let’s quickly skim through both to better understand the reorder point.
Daily Sales Velocity
Daily sales velocity, or in other words, the average number of units sold each day, varies depending on what you sell. Understanding that each item or product in your stock has a distinct sales velocity is essential. You may have a product that constantly sells, making you supply it more frequently and in larger quantities than other goods.
Moreover, specific goods may sell quicker during certain seasons, leading your sales velocity to increase momentarily. To determine a product’s reorder point effectively, you must first understand the abovementioned factors and how they may affect your sales velocity.
Lead Time
Another major factor for understanding reorder points is lead time. It is time it takes for an ordered supply to arrive from your supplier. Supplier delays can cause issues with inventory management, resulting in a shortage of your goods. Delays can have drastic effects, especially when it comes to popular items. Not being able to deliver demanded products on time can negatively influence your company’s public image. It can also negatively affect customer reviews. Moreover, if the client service starts to deteriorate because of delays, your customer base might choose your competitors with more dependable and constant inventories.
How to Calculate Reorder Point and Safety Stock?
Keep in mind that if you purchase products and items too soon, you will have extra inventory that will cost you money to keep.
On the other hand, you risk running out of stock and losing sales if you order too late.
Reorder Point Formula
To determine a precise reorder level, you need accurate formulas to tell you when to restock. The procedure for determining your inventory reorder point is straightforward:
Reorder point formula= Lead time demand + safety stock
Lead time demand isn’t that easy to understand. It’s the average daily demand during lead time, so we need to calculate it separately before determining our reorder point formula. Lead time equals the sum of supply delay and reordering delay. In simpler terms, it’s time it takes to process an order and receive your supply. Reordering delay is the additional time needed for a company to place and process an inventory order.
Lead time = Supply delay + Reordering delay
Safety Stock Formula
To calculate safety stock, it is essential to have a purchase and sales order history. Once have the data on hand, you will simply need to utilize the following simple safety stock calculation:
Safety stock = (Maximum daily consumption * Maximum lead time in days) – (Average daily usage * Average lead time in days)
Precise calculations will help you determine how much safety stock you need on hand. Knowing how each factor affects your reorder point and safety stock, you can plan when to order inventory effectively.
Summing Up
Reorder point vs. safety stock debate can be quickly resolved when you understand the importance of each in inventory management. It is crucial for determining when to restock products, while safety stock ensures that you have a sufficient amount on hand to meet customer demand. By utilizing these formulas and understanding their effects, your inventory management will run smoothly and successfully.
Calculating and analyzing is crucial, but having a professional tool for workflow automation can make things easier for you. Check out our versatile inventory management software at eSwap. We offer a free trial to see if it is the right fit for your business. Happy inventory managing!