According to Wikipedia, safety stock is a phrase used by logisticians to indicate a quantity of excess stock kept on hand to avoid out-of-stock cases caused by market demand fluctuations. With sufficient volumes of safety stock levels, businesses can ensure uninterrupted operations.
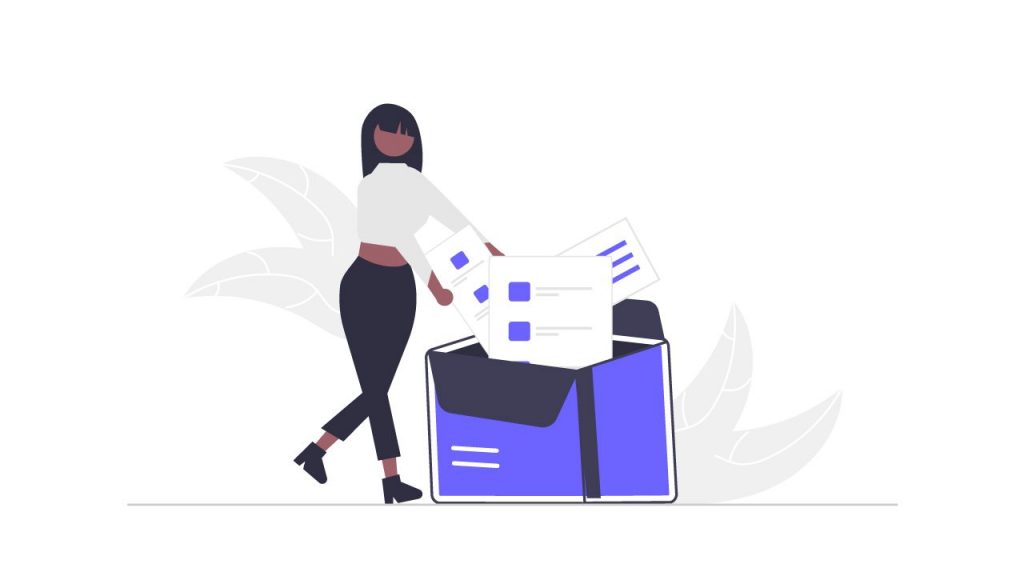
So, the primary cause that manufacturers and retailers ensure adequate safety stock levels exist is the prevention of possible stockouts. Common causes of stockouts include consumer demand fluctuations, inaccurate sale or stock forecasts, lead time delays by suppliers, etc.
Why do companies need a safety stock?
There are external factors that businesses cannot control. Demand and lead time uncertainties are the two main externalities that require retailers and manufacturers to protect themselves with safety stock.
Market demand uncertainty
Depending on the industry, there is a level of market demand predictability. When we think about products not generally affected by seasonalities or specific events, demand forecasts have relative certainty.
Let’s think about home appliances, such as a refrigerator.
Every home needs it in every season. So, its sales and demands can be easier to forecast because there is a demand consistency. Therefore, there might not be a need to hold high volumes of safety stock by hand. Of course, there are exceptions as well. For example, during big sales, such as on black Friday, sales may jump. For those cases, businesses still might need to secure themselves with extra stock.
On the other hand, there are products and industries highly affected by seasonal changes. For example, swimwear businesses face demand peaks in the summer months. So, to deal with uncertainties, they might choose to hold higher than forecasted inventory levels to avoid stockouts.
Lead time uncertainty
Operations of the companies operating in the manufacturing industry strongly depend on their suppliers who deliver raw materials and other components to produce goods. There the lead time plays a huge importance in setting inventory plans.
Sometimes, delays can make a huge impact, especially when companies have a just-in-time inventory approach. In this case, they receive materials right before they need to be used. So, the supplier’s lead time affects the manufacturer’s lead time and can even shut down the whole supply chain. To avoid these disruptions, it is reasonable to maintain safety stock for force majeure cases.
Safety stock calculation methods
Average – max method
The formula of the average – max safety stock calculation method is the following:
Safety stock = ( Maximum lead time x Maximum daily sales ) – ( Average lead time x Average daily sales )
Let’s look at the following example.
The sales department of Company XYZ provided the following statistical summary of the yearly sales based on which we should calculate the safety stock level.
The above data gives us sales units for 12 months, the total of which is 12,300. The daily average sales are 34 units. You can calculate it by dividing the total units to 365. To find the maximum daily sales, the highest monthly sales figure should be divided into 30 days. In this case, there are two months with 1,400 unit sales. So, the maximum sales will be 1,400/30, which is 47.
Additionally, during the 12 months, there were 10 deliveries with an average lead time of 19.4 days, which is the numerical average of the 12-month delivery date. As we see, the 7th delivery has the longest lead time of 24 days, which will be the max lead time figure.
So, to find the safety stock, we need to make inputs into the above-given formula:
Safety stock = ( Maximum lead time x Maximum daily sales ) – ( Average lead time x Average daily sales )
Maximum lead time: 24
Maximum daily sales: 47
Average lead time: 19.4
Average daily sales: 34
Safety stock = ( 24 x 47 ) – ( 19.4 x 34 ) = 1,128 – 659.6 = 468.4
So, based on the data above, the required safety stock volume is 468 under the average – max method.
The advantage of this method is its simplicity. However, even a rare variation such as an extremely long lead time that happened once can strongly affect this calculation.
Basic safety stock formula
Traditionally, specialists use basic safety stock formula to calculate safety stock. Based on that method, you need to have daily sale quantities of a particular product and determine the number of days you want to hold stock units. For example, if your daily sales are 10 units and you want to hold 10 days’ worth of inventory, you will need 100 units (10 units/day x 10 days) on hand as a safety stock.
So, the formula will be the following:
Safety stock = Average daily sales x number of safety days.
This approach is fundamental and does not consider many factors.
Tips to optimize safety stock
Following are some tips you can apply for better safety stock management and optimization.
- Integrate an automated system to avoid manual settings. The issue is that for manual tracking, usually safety threshold is set on a specific quantity. It is not dynamically updated by the change of sales figures. An automated inventory and order management system, like eSwap, will provide in-time updates of sales and orders data, giving reliable further calculations.
- Focus your attention on accurate forecasting rather than increasing the safety stock threshold. Reliable and timely data is the primary source for precise forecasting, which too can be achieved by statistical and analytical reports easily generated by software systems, such as eSwap.
- Instead of increasing the safety lead time, ensure that your suppliers follow deadlines.