In each field, terms are one of the various vital aspects. For people who are dealing with sales processes knowing the warehouse terms are significant. And it is of equal necessity both for retail and wholesale businesses. When looking for the right services and solutions for e-commerce, the wide range of warehouse terminology can seem confusing. That’s why here on eSwap, you can now find the most commonly used warehouse terminology with their definitions.
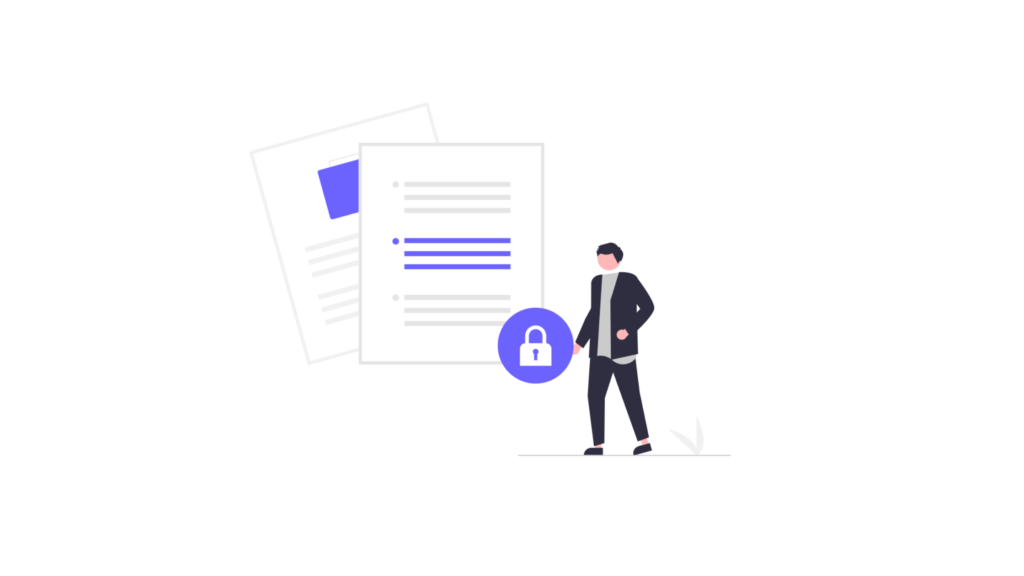
1. Days of Supply
The retailers use the following term as an element of warehouse terminology. It helps to estimate the average time (how many days) a company needs to sell its entire inventory. Inventory Days of Supply indicate the average period between the date of purchase and the date of customer sales. As for the manufacturers, it shows the average time between the purchase the raw material purchase date and the distributor sales date.
Inventory Days of Supply are calculated via dividing the average inventory by the COGS (Cost of Goods Sold) per day. The Average Days to Sell the Inventory are computed by dividing 365 (the number of days) by the Inventory Turnover Ratio.
2. Defective goods inventory (DGI)
A product can be defined as defective if it is dangerous in case of its intentional use. Let’s be more specific. A defective product harms people due to design, manufacturing, marketing or other faulty issues. Items of various categories and groups can be regarded as defective—for example, food items, clothes, medical devices, children’s toys, etc.
3. Distribution Center
Distribution centers are particular points that are concerned with the processes of storing and shipping. They are usually the places where the hence process of distribution is managed and handled to be organized. Distribution centers are where the workers store goods for later order fulfilment and shipping managed.
The majority of distribution centers have a storing area, loading dock and shipping section. Inventory goes the way through centers. Efficient work of distribution centers is the core of the whole supply chain workflow. The main components include Integration, Operations, Purchasing, fulfilment. Companies can have return policies, and in such cases, centers are involved with logistic and returning issues.
Distribution centers are the fundamental components of the majority of modern organizations. They make sure items reach the desired place at the precise time. Those centers grasp technologies to find solutions for complex processes. No matter it is the retailer, wholesaler or customer to get the order. All these are a crucial part of e-commerce.
4. Multi-Channel
Multichannel is mainly viewed as a part of warehouse terminology used in the field of marketing. It shows the way how products interact with potential customers throughout numerous channels. They can be both online and offline. Businesses have to establish those channels which their customers most probably will use. They then think out the strategies that can be the most straightforward and most attractive for use.
5. Vendor-Managed Inventory (VMI)
Vendor-managed inventory is a kind of inventory that suppliers or vendors organize and manage. This type of inventory involves another side except for the customer. And that’s him who takes responsibility for the inventory management components, like setting and managing, re-ordering, and replenishment of the listings.
6. Raw materials
It is the name of substances and materials used at the very beginning of goods production or manufacturing. People buy and sell the items of raw materials worldwide as they are also parts of production like labour and their products. Usually, this process happens in the production factors. Raw materials are a crucial part of the supply chain. Businesses use it as an inseparable part of any product. They can appear in various forms. They require detailed budgeting and special attention.
7. Gross Margin
Gross margin is the revenue that companies get after acquiring the direct costs associated with goods production. As costs, a company sells it, as well as provides services. GM is a metric calculated by taking the company’s net sales revenue out of the cost of goods sold (COGS). If the gross margin is high, then the capital of that company is higher as well. The businesses can later use it to pay additional costs.
8. Holding cost
Holding costs are the costs that are associated with inventory storage and maintaining. Especially those that the businesses have not sold yet. They are total inventory costs’ major component apart from shortage and ordering costs. Holding costs involve the price of damaged or spoiled goods. And also the prices of space needed for storing goods, labour and insurance. In supply chain management, one of the most crucial points is holding cost minimization. As for requirements, it requires a significant cash outlay. Decisions regarding inventory spendings can lower the money that can be spent on other issues with other purposes.
9. Backorder
A backorder is a kind of order (good, service) the fulfilment of which can’t happen immediately. It can happen because of supply or a time which are not enough. The item can still be in the process of production but non-available in stock. In this case, the company needs to produce more of the product in a shorter time. The backorder indicates demand that is higher than the amount of the supply. The numbers have a direct influence on the period and customer satisfaction level.
10. Lead time
Lead time is the total time, the duration of which is between the start of a process and its end. Companies highlight lead time for various operations. For example, manufacturing, supply chain management, and project management. It can take place before processing, right during the processing and after the processing steps. Reducing lead time helps in operation management. It also improves productivity, elevates output and revenue. And consequently, if the lead time is long, it negatively influences manufacturing and sales processes.
This is just a part of the rich list of warehouse terminology. eSwap will help you understand all of them with this type of articles making your efficiency in the world of e-commerce higher. Rely on our platform, keep reading our helpful articles. They will help to organize your best management experience with eSwap.