Anyone doing an eCommerce business should be related to certain warehouse management terms. As long as the range of the terms is wide and various, it’s quite possible to get confused. This is relatable, especially for those eCommerce sellers just starting to use inventory management.
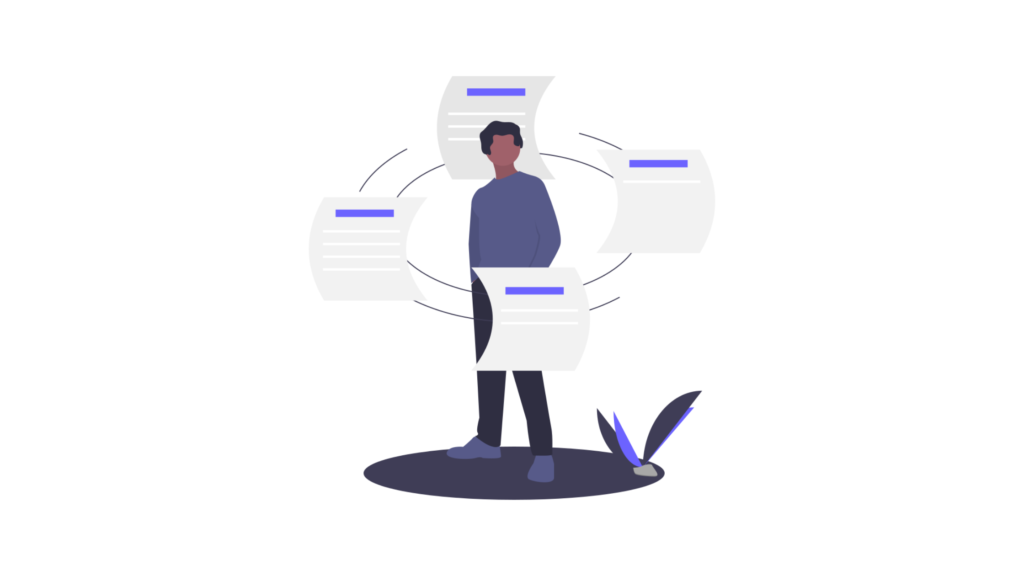
The proper knowledge of your warehouse management terms will allow you to have better control. It refers both to your internal and external communications.
Today, we will introduce you to another list of warehouse terms to gain better supply chain excellence in your field. Click here to find out more warehouse management terms.
Warehouse Management Terms: Key Performance Indicator (KPI)
KPI or Key Performance Indicator allows the businesses to understand a company’s effectiveness according to business objectives they set. KPIs express a company’s success in a measurable value. There are two main types of KPIs – low-level and high level. The high-level KPIs focus mainly on the overall business performance, while the low-level KPIs focus on different process departments.
Different KPI types are depending on the business type. These include Business, Financial, Sales, Marketing and Project Management types. As for the warehouse KPIs, they differ also. Putaway cycle time, picking accuracy, order lead time are a few of those KPI examples.
Warehouse Management Terms: Kitting
Warehouse kitting is the process of gathering different SKUs in one individual package under a single SKU. The kits work effectively, especially for the cases when the customers order multiple yet relatable items. Kitting is a form of an order fulfilment process.
There are multiple benefits that warehouse kitting may offer- including reduced labour costs and a less costly order shipping process. If there’s a possibility to send packages via kits, there’s no need to hesitate.
Apart from the mentioned benefits, kits help improve workplace safety and free up a lot of space in your warehouses.
Warehouse Management Terms: Handling Costs
Order handling costs refer to the expenses that the sellers ask the customers to pay to arrange the product order fulfilment process. It refers to the costs related to preparing and delivering the orders. The expenses which the buyers pay cover the shipment and packaging costs.
As long as the customers are mostly unwilling to pay for extra costs, it would help if you tried to make the proper calculations. It refers to your order handling fees firstly. It refers also to the order packing and shipping costs.
Warehouse Terminology: Parcel Shipment
The parcel shipping process refers to the delivery of small-sized boxed products. Parcels are packages that usually weigh under 100 pounds. This is to say the delivery doesn’t demand a lot of resources for parcel shipping. Parcel shipping is a good option for economical freight shipping. This form of order delivery option is good, especially for small businesses. It allows them to manage speedy overnight shipments with low freight costs. Besides, it will enable the sellers to ship products directly from the drop-off locations.
Economic Order Quantity
The Economic order quantity or EOQ is referred to the number of units that a company adds to inventory with each order. In that way, the company helps itself to minimize the total costs of inventory, referring to holding costs, order costs and shortage costs.
With the help of EOQ, companies usually can calculate the appropriate reorder points, which are exceptionally important for small businesses. That’s a kind of method you can apply to get optimal reorder quantities for your inventory. This is how you can make sure you will not end up with inventory shortages or overstocking.
EOQs help the sellers make appropriate decisions about the number of items they should keep or order each time.
Perpetual Inventory
Continuous or perpetual inventory management gives real-time stock updates. This system is the ultimate choice for huge sellers. As long as they have large sales volumes they need to keep the data accurate. The sellers who have low sales volumes choose the Periodic systems.
You can easily check the number of your stock left in the warehouses with this system. Each time you make transactions, the financial data gets updated. That’s the way the Perpetual system works. Consequently, you don’t need to stop your overall business operations to get that data. Above all, it helps to have the right inventory levels.
Obsolete Inventory
Obsolete inventory refers to the stock which cannot be sold for a long period of time. Therefore it becomes deadstock or excess inventory. Retailers try to do their best to avoid the cases of obsolete inventory. Therefore most huge businesses rely on inventory management tool like eSwap is.
This kind of software allows the sellers to avoid not only dead stockings but also overstocking and stockouts. That’s possible due to the software features like Warehouse Management, for example. It allows the sellers to reduce the manual operations and have real-time stock updates.
Besides, it allows to management of multiple warehouses from one dashboard. You can add, manage multiple warehouses and locations. eSwap allows an auto-creation of individual warehouses per sales channels also.
Work in Process (WIP)
Work in Process inventory is the type of goods that are partially finished to be on sale. There are some other terms referring to the work in process inventory like goods in process or in-process inventory. WIP in other words represents the materials that have started the production process but are not fully done yet.
As long as the WIP represents a company’s current asset on the balance sheet, making calculations for it matter a lot.
POS
The Point of Sale or a POS in other words is used to execute payments for goods or services which the customers purchase. POS systems are the combinations of both hardware and software to process the transactions. The POS software is the first component of the POS systems. The hardware is the equipment allowing to make a sales transaction. It may be a POS terminal, barcode scanner, credit card machine, etc.
The sellers traditionally set up the POS terminals near the exits of the brick and mortar stores. They believe it increases the rate of impulse purchases as customers leave.
m-Commerce
This is another widespread term in the world of eCommerce. It refers to mobile commerce. M-commerce allows executing ecommerce sales via wireless equipment like mobile devices such as smartphones, smartwatches, tablets and laptops.
Supplier-Owned Inventory
This is a type of inventory management model when the vendor takes full responsibility for the stock. It’s also known as SOI inventory management. The buyers provide the required stock numbers.
Packing List
Packing lists are mainly used in international trade. These documents provide detailed information about the contents of a package. It usually includes the description, quantity and weight of the goods. It’s the seller’s responsibility to prepare packing lists. The packing lists don’t include the prices of the items. There are other names also referring to the packing lists. You may hear a term like the bill of the parcel, unpacking note or a delivery docket.
Ordering Cost
Ordering costs refer to the expenses which are needed to pay to process an order to the manufacturers. There are different types of ordering costs. These might include the expenses to prepare purchase requisition or purchase orders. The ordering costs refer also to the labour costs for inspecting the goods while they arrive.