The proper running of warehouses of all sizes depends on precise warehouse optimization. Warehouse optimization is a systematic process that entails automating processes. It is aimed to determine ways to save time, space, and resources. Besides, warehouse optimization minimizes mistakes and boosts flexibility, communication, and management while meeting customers’ needs. All internal operations inside the warehouse must be as precise and efficient as possible. This ensures prompt order fulfillment for the end consumer and lowers costs due to a well-functioning supply chain. Warehouse optimization enables businesses to make the most of their space to create a productive and lucrative environment.
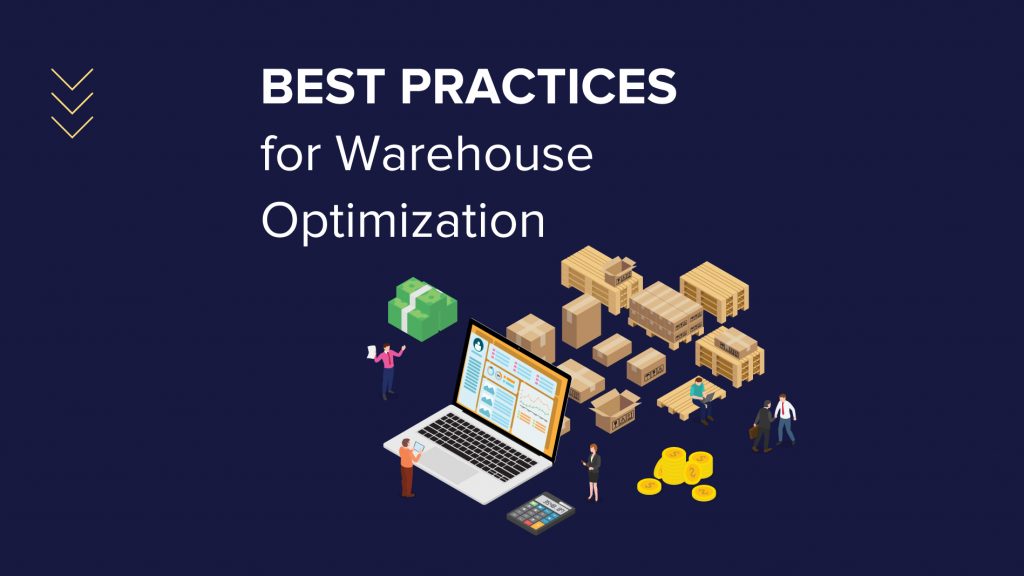
Why Is It Essential to Optimize the Warehouse?
Optimizing the warehouse management system is crucial for cost mitigation, precise planning and forecasting, enhanced customer service, and your business’s growth. Below find some of the benefits of warehouse optimization.
Enhanced Performance
Warehouse optimization should lead all internal operations, whether a company is new or experienced. Optimization can help streamline the inventory management approach for companies with functional warehouses. It also enhances areas that aren’t working to their full potential. For Startup companies, having a precisely operating warehouse can lay a solid basis for a firm’s future success and growth.
Reducing Costs and Errors
It is vital to understand that companies lose money daily due to incorrect shipments, refunds, erroneous inventory counts, and other errors. Every error costs an additional expense, which can be avoided with an optimized warehouse management system. Warehouse management software combined with an inventory management system may solve these inefficiencies and reduce errors. In fact, barcode scanning can solve many issues.
Improved planning
Warehouses can better plan for the future by being able to anticipate and forecast inventory requests. This information makes it simpler to distribute resources without incurring additional expenditures.
Providing Excellent Customer Service
Customer service is crucial for the long-term success of your business.
When a warehouse is optimized, it creates conditions for high-demand products to be constantly supplied. This leads to timely order fulfillment. With an automated system in place, with a smoothly running inventory flow system, improved inventory procedures, and speedier packaging and delivery operations, your business will achieve higher order fulfillment rates and meet the demands of your customers.
What Are Some of the Most Efficient Warehouse Optimization Practices?
Below find a list of warehouse optimization practices to enhance the performance of your business.
Make the most of your warehouse’s layout and storage
Determining the best storage place for each product in your inventory is known as warehouse slotting. Slotting optimization enables warehouse workers to pick items faster, allowing for next-day or same-day delivery, a popular e-commerce option. This way, you will ensure that you get the most out of your storage space. It is nearly impossible to optimize warehouses manually as it will require you to examine a large amount of data. Therefore to make sure that you save your time and resources, it is essential to invest in warehouse optimization systems.
When calculating the storage space, make sure that you consider all warehouse operations, including obtaining stock, maintaining things in storage (with extra space for anticipated growth), and incorporating room for at least one day’s worth of orders in advance staging, and shipping and for returns.
Take advantage of automation
In order to eliminate mistakes, it is crucial to automate the receiving process with warehouse management software. It is essential to understand that when receiving products manually, an employee examines a shipment invoice and visually verifies that everything indicated on the invoice has arrived and is in the correct quantity. This approach is less expensive, but it raises the risk of human mistakes. Therefore, double-checks are frequently necessary, increasing your company’s expenses. You may eliminate errors and save time and money by automating this process using warehouse management software. By simply scanning product barcodes using automation software, you may upload all of the data to your server.
Workflow automation is easier than ever before due to modern, advanced inventory management systems that will do the work for you. With eSwap software, you will be able to automate all of the routine duties. Due to this feature, order management-related repetitive chores can be easily automated, making your job easier and more efficient.
Create efficient inventory replenishment procedures
Inventory replenishment procedures can become less stressful and time-consuming with an effective inventory management system installed. With an optimized warehouse management system, you will be able to meticulously manage your inventory replenishment by forecasting the demand and carefully analyzing your inventory data. It is crucial to find the golden middle and have enough inventory to fulfill a need while avoiding overstocking things that won’t sell or won’t sell enough to optimize profitability. eSwap will provide you with valuable out-of-stock or low-stock information, which will automatically help you avoid manual stock level updating and have up-to-date data on product quantities. This way, you will avoid out-of-stock situations, get notified in case low stock occurs, and get daily reports and notifications to be in charge of your inventory.
Optimize the shipping process
Remember that one of the essential aspects of enhancing customer service is being able to deliver the products to your customers swiftly. Assuring that packed items are delivered to the right pickup place is crucial in the order fulfillment process. Instead of depending on human labor, order routing automation can significantly speed up the process. Due to eSwap’s automated shipping workflow, you will be able to manage every stage of your shipping process. This includes adding and editing dates for shipping orders, easy barcode scanning, and setting or removing default shipping label templates.
Moreover, with modern inventory management systems, you will be able to compare and choose the best shipping carriers by delivery time, insurance, delivery attempts, and shipping rates. eSwap can also allow you to find all significant worldwide shipping carriers. This includes UPS, FedEx, USPS, DHL, etc., allowing you to have several alternatives in one platform.