Inventory is an asset that a company uses in production or sales. For many companies, inventory is a crucial asset because of its high value and profit-generating nature. That is why business leaders invest in inventory management processes and tools to improve inventory practices and business performance.
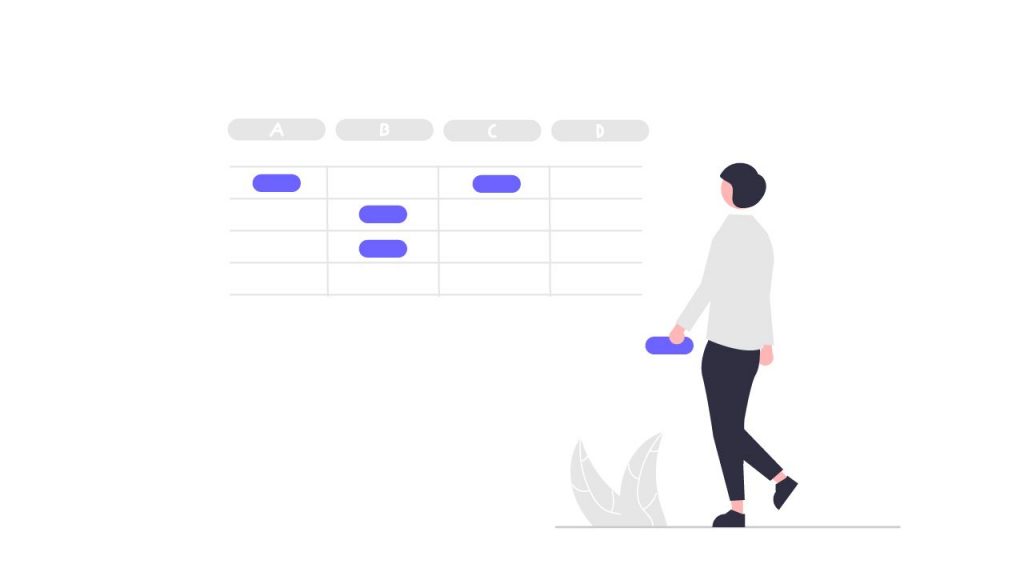
What are the 4 types of inventory?
Inventory has four general groups:
- raw materials
- work-in-progress (WIP),
- finished goods and maintenance,
- repair and overhaul (MRO).
It is essential to know about four common types of inventory and their moving patterns for cost-effective supply chain management.
Raw materials
As the name itself suggests, raw materials represent the essential substances that companies use in manufacturing processes to develop final products. For example, aluminum, steel, rubber, and plastic are the most used raw materials in the automotive industry for car assembly. Different types of fabrics are the primary raw material in the textile industry.
Usually, the final products of one company are the raw materials for the other one. As for the example mentioned above, companies producing aluminum sell it as their final product to automotive manufacturers, which is used there as a raw material.
Optimal management of raw materials is extremely important. Depending on an industry holding high raw material inventory levels might create a risk of perishment and expiry of materials. As a result, they not usable in production and will just make costs for the business. The opposite scenario of holding low inventory levels also has risks, such as the inability to meet market demands. Thus, optimizing raw material volumes is very crucial for businesses.
Work-in-progress (WIP)
Also known as semi-finished goods, work-in-progress stock are raw materials that are about to undergo conversion into the final products. They are mid-processed raw materials lying on the production floor and will be converted into finished goods eventually.
We suggest you to keep work-in-progress inventory volumes low because generally, they have no use until conversion into the finished goods. Although it might be possible to sell them at some price, it is usually not enough to generate any income for the company. In lean manufacturing business work in progress, inventory is actually believed to be a waste.
So, the best practice would be to minimize both the volumes of work in progress inventory as well as the time it takes to move them to the process of final goods production. The shorter that time is, the faster the locked-up value will be realized. The locked-up value is capital that could have been otherwise invested in other assets and generate better returns.
Finished goods
Companies invest in raw materials and work-in-progress inventory to later use it in producing finished goods, which are the final products of the business. Finished goods are ready for sale products which are the primary income generators for the company.
There are two general types of industries depending on the volume levels of finished goods.
- First, let’s discuss the industries with mass production of final products. Such examples are fast-moving consumer goods. Companies in the FMCG industry should adjust their inventory levels to market demand.
- The other type of industry is those that initiate a production upon receipt of an order. An example of this can be real estate companies or customized goods industries which start productions based on the orders. These companies should not hold any finished goods because customer’s preferences are of core importance, and the slightest deviations can lead to order rejections.
Maintenance, repair, and operating (MRO)
MRO represents those consumable materials, supplies, and equipment used in the manufacturing processes of final products but is either not a part of them or a tiny one. Examples include personal protective equipment, cleaning supplies, office supplies and furniture, technological equipment, tools, industrial equipment, etc. Even though MRO inventory is responsible for the 5-10% of Cost of Goods Sold (COGS) amount, companies are not monitoring its expenses. However, proper control over MRO resources, such as audits, pricing negotiations, cost-cuttings from unnecessary usage, can reduce these costs.
Types of inventory management systems
Because of its nature and value, inventory is an asset that requires proper control and monitoring. To do that, companies use one of the two main inventory management systems.
Perpetual inventory system
Perpetual inventory systems perform on-time updates of inventory balances and accounts. Each movement and sale, addition, or subtraction of the stock is is under the right on time recording. Many companies prefer this perpetual inventory system because of the timely updated data and minimized necessity or physical inventory counts. They also ensure the high accuracy of results. Inventory management apps and software are perpetual inventory systems. Issues with this type of system include the requirement of software and equipment and costs associated with them, the necessity of continuous upgrades and maintenance, etc.
An example of a perpetual inventory system is eSwap software, which provides in-time order and inventory management features. With the synchronization of multi-channel platforms, the inventory data is always accurate and fresh.
Read more about what is perpetual inventory system and what you should know about it.
Periodic inventory system
As the name suggests, Periodic inventory systems provide companies with stock data at the beginning and end of specific periods. Physical inventory counts are conducted in these inventory systems, after which the balance shifts from purchases to inventory accounts.
Periodic inventory systems have some disadvantages. During the physical inventory counts, the business activities are on hold. This speeds up workers, which might increase the potential of errors. Also, when business operations are on hold, the company does not work and generates revenues. Moreover, there might be significant changes in inventory amounts between counts.